一体化系统中的核心问题 一体化生产管理系统分成订单排产和作业计划两个阶段.订单排产阶段是把接受合同订单的明细,整理为具体的生产批量,是生产计划的组织阶段,系统不仅考虑合同内容,而且还要考虑各工序的约束条件、效率、库存、制造标准、交货期等,做出目标最优的生产计划;作业计划阶段是把生产计划按详细作业展开,为此把各工序按时间序列细分,计划延迟或工序发生异常时,系统则进行实时的动态调整。
2.1 订单排产阶段
基于高级计划排程(APS)思想的一体化系统中,计划功能用于确定在特定计划时间的范围内来满足制造系统的需求.对计划过程的输入内容包括与需求数据和制造能力相关的信息,如客户订单、已下达的生产订单、安全库存的需求、物料清单、各个工序能力的可用性及零件工艺,同时也考虑库存量、已计划交货量.计划过程的输出是一个可行性的计划,每一个计划的最终物料订单都具有一个承诺日期,该日期是通过订单可承诺量ATP和可承诺能力CTP确定的。
(1)ATP库存匹配模型,库存匹配工作是生产计划编制前对订单的预处理过程。它有利于提高产品的及时交货能力、解决库存造成的资金和场地占用问题,在钢铁等流程工业中普遍存在。本文假定订单已进行了拆分,即每个订单只包含一种规格求的产品。这样,库存匹配问题可以简要描述为:给定N个产品,M个订单。要求找出尽可能多的产品在满足规格、重量等约束的条件下与订单进行匹配,使匹配的重量最大化。在产品与订单进行匹配时,必须符合订单的规格要求.除了规格要求,还要考虑同一个订单匹配的产品重量之和不得超过该订单所要求的重量。
为了便于建立数学模型,首先定义相关符号:i为订单序号,i=1,2,3,...,M,M为订单总数;-j为产品序号,j=1,2,3,...,N,N为产品总数;Oi为订单i的重量;wi为产品_j的重量;Ωi为符合订单f的规格要求的产品集合;Xij为0或1,若产品,j与订单i匹配则其值为1,否则为0。
利用上述符号。可以将库存匹配ATP模型表述为:

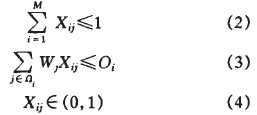
模型中。式(1)所描述的目标函数指与钢卷匹配的订单重量最大化,式(2)~(4)为其约束条件式(3)表明与同一个订单匹配的产品重量之和不得超过该订单要求的重量,式(4)表示变量的取值范围.
(2)CTP能力匹配模型.ATP模型意在最大限度地利用库存产品对客户订单需求做出及时和准确的反应,缩短交货提前期、降低库存水准.对在ATP系统中没有得到匹配的订单,需要通过能力匹配模型来进行排产。并根据排产结果给出交货期承诺.在该领域也有一些相关研究,例如文献[4]建立了合同计划编制的整数规划模型,提出了基于可重复自然数编码和三变异算子的遗传算法对模型求解;文献对订单计划做了综合考虑劳动力成本的长期规划模型.钢铁生产的主要流程为炼钢一连铸一热轧一冷轧一镀锌等,在订单生产中,并非所有的产品都要经过所有工序的加工。最终产品可以是钢坯、热轧卷、冷轧卷、镀锌板等.因此在实际的订单生产中,可能包含多种产品类型.本文在考虑不同订单对加工工序的特殊要求的基础上,综合考虑了设备能力平衡、利用效率最大化和工序顺序约束,提出以交货期偏离惩罚最小为目标的单目标整数规划模型,订单排程计划应使所有的订单拖期/提前惩罚最小,并且满足设备能力约束和前后工序之间的时间约束。
钢铁企业的订单排产计划编制可概括为:给定J个订单、K种工序,每个订单的产品种类可能不同,每种产品要经过若干工序的加工;订单的拖期会导致拖期费用并使企业信誉下降,而订单的过早完成会导致库存费用的增加;由于钢铁生产工艺的特殊性,在生产过程中。工序之间存在着特殊的时间约束(例如,连铸和热轧工序之间最长不能超过一定的时间间隔,而热轧与冷轧之间则必须经过一定的冷却缓冲时间等),在本文中称之为最大等待时间和最小缓冲时间.钢铁企业的订单排产计划应使所有的订单拖期/提前惩罚最小。并且满足设备能力约束和前后工序之间的时间约束。
本文建立的基于能力约束的订单排程模型基于以下几点假设:(1)生产模式为订单交货期驱动型;
(2)每道工序中的每台设备在一定时期内加工能力一定并已知;(3)某种类型的产品在各个工序上加工时间一定并已知;(4)不单独考虑中间库存与订单分割;(5)前序工序的生产能力大于后继工序.除了设备能力因素.其他生产资源的限制不被考虑。
为了便于建立数学模型。相关符号定义如下:T为对象生产周期,所有订单都在时间段T内完成;i为订单序号i=1,2,...I,I为定时期内的订单总数;n为工序序号,n=1,2,...,N,N为工序总数;Xin。为订单i在设备n上的开工时间;tin为订单i在设备以上的加工时间;bn为工序挖与,n+1之间的最小缓冲时间;gn为工序n与n+1之间的最大间歇限制;di订单i的交货期;Cn为工序n的设备加工能力(一定时期内的最大工时)。在本模型中认为Cn 利用上述符号,可以将CTP能力匹配模型表述如下:
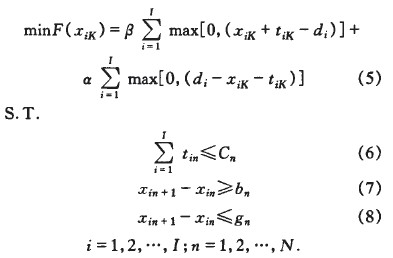
目标函数(5)是最小化所有的订单提前/拖期总惩罚值。式(6)~(8)为其约束,约束(6)保证一定时期内所有订单的相应产品在相应设备上的加工工时不超过该设备在此时期内的最大加工能力,约束(7)和(8)保证工序间的缓冲.由于钢铁生产过程的特殊性,对于一种产品的加工。后继工序可能必须在前序工序完成并进行一定的缓冲后方可开工。此种情况适用约束(7);也有可能后继工序与前序工序之间不能超过一定的时间间隔,此种情况适用于约束(8)。
2.2 作业计划阶段
基于APS思想的一体化系统中计划排程模块的作用是生成工序的详细作业排程清单,以指定何时在哪道工序上处理哪个订单.系统的计划排程功能是以订单为中心并由彝件驱动的,在一组订单及其相关开始日期已经确定的情况下,由计划排程模块算法生成时间顺序列,即一个包含每个订单首道工序的时间顺序列表.因为该工序能够获得它所需要的设备能力和物料,因此将更新该时间序列反映工序结束的时间.随着时间的推移每个订单都会完成其路径,其截止日期取决于系统的动态设置情况,订单在系统中经过的最终结果是一个详细的时间表。
(1)CCR——冷装工艺:炼钢一连铸生产调度,一般意义上炼钢一连铸生产调度问题可以抽象为混合(hybrid)流水车间的作业排序问题,此类问题已被证明是NP一难题.炼钢一连铸生产调度需要协调冶炼、精炼和连铸三个作业工序的生产节奏,在满足对钢水温度和时刻的要求、保证生产持续性的前提下,充分利用有限的设备资源。
炼钢一连铸作业计划问题可以归结为一个混合整数规划模型,其目标为最小化浇次的断浇次数和炉次的等待时间.由于各种变量数目巨大,因此直接对模型进行求解是困难的.文献将此问题分解为两个子问题。先探讨炉次设备指派的策略,为炉次指派设备、生成粗调度后。再用一个线性规划模型来确定各炉次最终的开始处理时间,以解消可能在的设备冲突。
(2)CCR——冷装工艺:热轧生产调度.轧制批量计划的编制,主要有两种解决方案:一是采用基于旅行商(TSP)模型的串行策略;这种方法动态性虽强,但结果可能是局部最优而非全局最优.二是采用基于车辆路径问题(VRP)模型的并行策略;这种方法计算虽然复杂,却能保证整个轧制计划全局最优。
轧制阶段的批量计划(轧批)的主要约束在于宽度和厚度:宽度必须按规则变化(双梯形结构);厚度必须平滑变化,其目标是:①保证产品厚度方面的跳跃最小;②保证产品宽度方面的跳跃最小;③整个批量计划包含的板坯数应尽可能多.考虑到编制轧制计划时,并非一次将所有板坯编排完,调度员首先向系统输入需要编制的轧制计划数,然后由计算机根据资源状况和约束条件从板坯库中选出板坯进行组批和排序,因此将问题归结为确定车辆数的车辆路径问题。
(3)HCR——热装热送:炼钢一连铸一热轧一体化的生产调度.基于炼钢一连铸生产调度模型、热轧生产工艺、板坯和炉次对应关系及JIT思想建立的一体化生产调度模型须满足以下条件:①批量计划(炉次和轧制单元)已编制;②不改变子调度前后顺序;③每台轧机同时只能加工一块板坯.炼钢一连铸一热轧一体化生产系统的调度问题实质是,在批量计划(炉次、浇次和轧制计划)的基础上,以炉次(或板坯)为最小计量单位,追求某一评价函数最佳情况下一类多工件、多工序、多机的特殊的ob—shop排序问题.其目标为板坯提前和拖期惩罚费用(保证板坯准时交货)、连轧断开损失惩罚费用(保证同一轧制单元中的板坯连轧)、板坯等待处理时间的惩罚费用等四个部分的总费用之和最小.炼钢一连铸生产调度模型是以炉次为最小单位,而热轧生产调度是以板坯为最小单位.为便于求解。采用了拉格朗日松弛法对模型分解,使原调度问题分解为两层优化,上层优化拉格朗Ft乘子,下层用动态规划求解子问题,使求解得到很大简化。
(4)冷轧.冷轧产品(宽带冷轧板、镀锌板、彩涂板等)是钢铁企业的高附加值产品,其生产过程具有多产品、多流向等复杂物流特征.为保证生产线连续运行,需要对存在着复杂供料关系的上下游机组之间的工料关系进行有效地协调.由于设备使用状况、工艺限制、库存容量以及初始库存量等诸多因素的影响,冷轧生产作业计划的编制以及物流控制是钢铁企业生产计划与调度领域的重点和难点问题,目前多数企业仍采取人工判断和调整方法进行冷轧生产的组织和管理。
冷轧生产作业实现均衡生产和优化生产计划与调度控制很困难,这是因为冷轧生产线既有串行生产线的均衡生产问题,也有离散生产的排产与调度问题;它既要协调各车间机组的排产作业计划,降低酸洗冷轧联合机组切换频率。也要保证连续生产前提下降低酸洗冷轧联合机组和后续机组的中间库库存;它不仅涉及到冷轧企业内部的优化运作模式,而且还存在与上游热轧间的协同计划问题;其复杂性还体现在既有离散计划调度的复杂度。还有流程企业对实时性的要求。
因此,根据冷轧生产系统中原料种类繁多,工艺路线复杂,且同时须兼顾设备和工艺限制等约束条件的特点,认为建立面向订单的、确保生产连续运行的、能够降低酸洗冷轧联合机组切换频率和中间库库存水准的计划模型,是冷轧生产计划管理的关键。
3 结论
本文在对钢铁企业信息化体系结构及生产管理模式等进行理论研究的基础上,针对钢铁企业生产的具体特点,提出了面向订单的钢铁企业一体化生产管理模式和体系结构。采用基于APS高级计划排程的思想来构建现代钢铁生产过程中面向订单的一体化生产管理系统和解决方案,同时分析了钢铁企业生产流程各阶段的先进生产计划方法和动态实时调度策略.为进一步展开研究,开发能够应用于钢铁生产实际的实用算法提供了系统框架和理论基础。